We wanted to add two rear windows and two side windows. One behind the drivers seat and one in the sliding glass door behind the passenger seat.
First - it was very hard to find the part numbers. I finally used Safelite to order the windows from and do the installation. The only issue (issues abound) was that they do not cut the holes. So I had to do that. Not particularly hard but NOT for the faint of heart.
Best tool to use is a Bosch jig saw with very fine (30-35 point teeth I think) saw blade. I tried a sawzall but it is to inaccurate. My advice is to make a pattern and lay it out on the outside using pilot holes lined up by drilling from the inside.
Use tape to protect the finish and make sure you spray silicone on the bottom of the jig saw.
Have at least 3 spare saw blades. Never extract the blade unless it is fully stoppped. Use a sharpie. Measure three times - cut once. Make sure you can see what you are doing. Use safety glasses, ear protection and a dust mask.
Rear windows are different sizes and you use the outside of the raised area. Drill pilot holes and then lay it all out on the outside.
Cut slowly and use a small ladder.
Once done use a file to smooth rough edges and then prime the raw metal.
Safelite had some cool black primer. It dried fast.
We then installed the trim lock edge material to give a finished look. The interior hook was on the inside so the outside was smooth and flat.
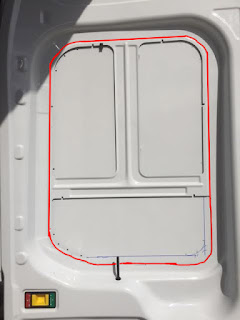 |
Left Window - do not cut off the lock pull |
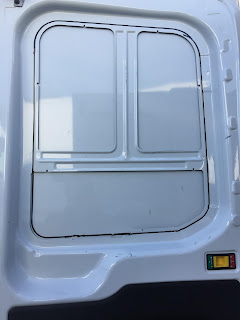 |
Right Window |
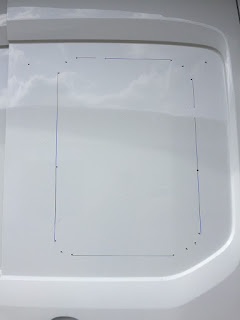 |
Notice the pilot holes - this is what you use to draw straight lines on tape. The tape needs to define the outside of the hole. This protect the paint. No need to protect inside the line as you are throwing that away. |
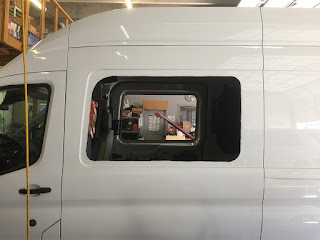 |
Completed cut on drivers side |
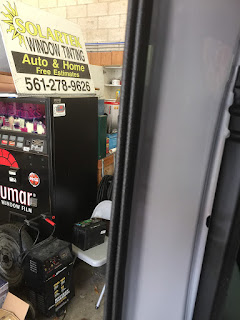 |
The back windows needed only a single Trim Lock. The sides needed two. One for each sharp metal edge. |
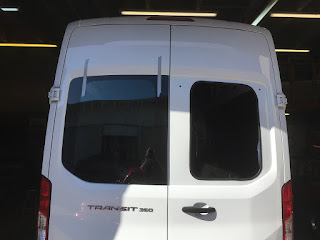 |
One window in - three more to go. |
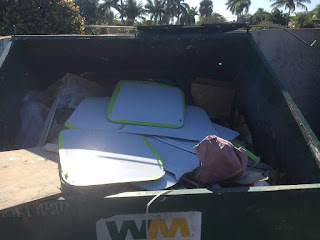 |
The excess metal tossed away - careful - very sharp |
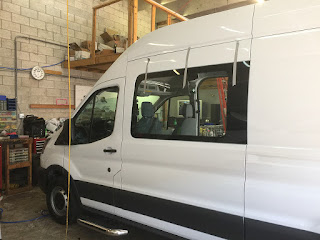 |
Drivers side glass installed |